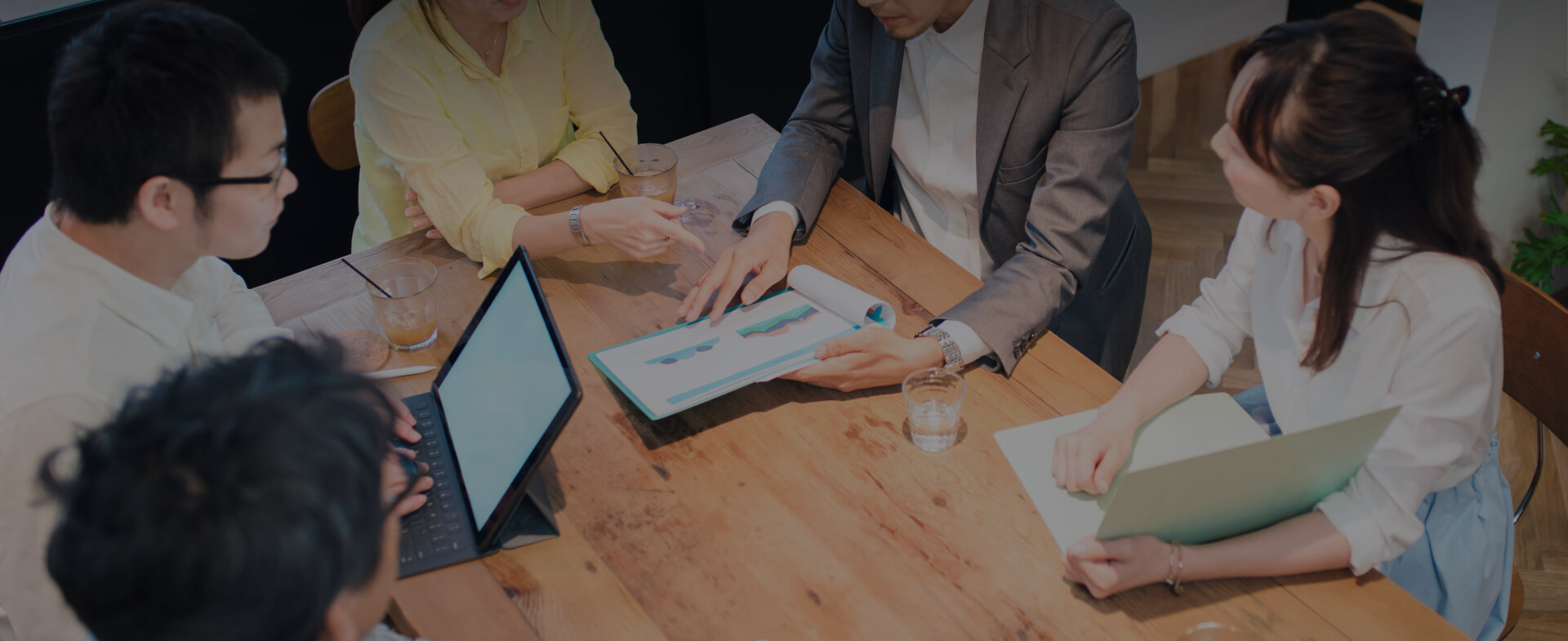
Corporation Social Responsibility
Fulfill carbon reduction, build green homes, emphasize environmental education
Occupational Safety and Health Management
Implement safety and health education and training every year to ensure that all employees can perform safe operations with safe behavior and a safe environment. Formulate safety and health inspection operations, and take practical actions to inspect and to inspect various operations any time to prevent and prevent disasters. Establish a series of disaster emergency response procedures to protect the lives of employees and manufacturers, as well as the property interests of company investors, and to avoid or to reduce the impact on the families, society or environment when accidents or disasters occur.
Statistics of Lost Time Rate and Work Injury Rate of Suao Plant in the Past Three Years
Project | 2018 | 2019 | 2020 | |||
---|---|---|---|---|---|---|
Gender | M | F | M | F | M | F |
Work Injury Rate IR | 0 | 0 | 0 | 0 | 1.87 | 0 |
Occupational Disease Rate ODR | 0 | 0 | 0 | 0 | 0 | 0 |
Lost Time Rate LDR | 0 | 0 | 0 | 0 | 201.44 | 0 |
Absence Rate AR | 0.00119 | 0 | 0 | 0 | 0.84 | 0 |
Total number of work-related fatalities | 0 | 0 | 0 | 0 | 0 | 0 |
Note:
1. Work Injury Rate IR=(Total number of work-related injuries/total working hours)*200,000
2. Lost Time Rate LDR=(Total lost days/total working days)*200,000
3. Absence Rate AR=(Number of days absent/total days of attendance)*100%
4. 200,000=According to 50 weeks per year, 40 hours per week, the rate per 100 employees.
Work environment and employee safety protection
The company's safety and health management is "people-oriented". Any mechanical equipment and plant configuration in the operating environment must first consider the essential safety of the equipment, the humanized consideration of configuration design, adequate equipment safety protection facilities and personal protection The equipment is provided to prevent and protect the safety of personnel in advance. The dust, noise and specific chemical substances in the working environment are all considered in the process design, and the hazard is minimized by engineering design, and supplemented by the standardization of personal protective equipment and operations to reduce the time for employees to contact the hazard source To ensure the safety of employees.
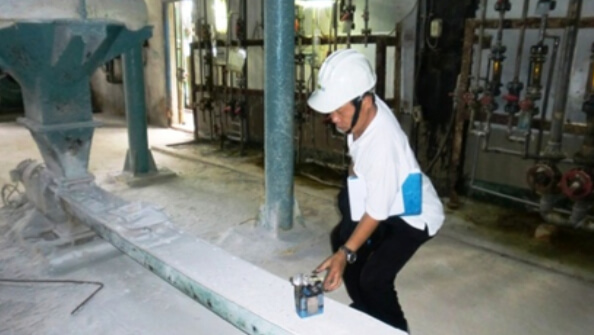
General safety management, training and audit
The company implements various safety and health management operations, such as: process safety and health management, machinery and equipment automatic inspection management methods, safety work permit implementation rules, subcontractor management methods, contractor management, work environment determination, hazard communication, Safety management and auditing of TPM system inspection, zero-disaster reward and punishment operations, and safety and health inspections.
Draw up an annual education and training plan every year, as required by laws and regulations, implement relevant safety and health education training and emergency response drills for in-service employees, implement in-service retraining operations for special operations personnel, to ensure that employees comply with the new laws and regulations . In addition, the relevant workers are provided with more than three hours of education and training on hazardous materials and hazardous materials each year.
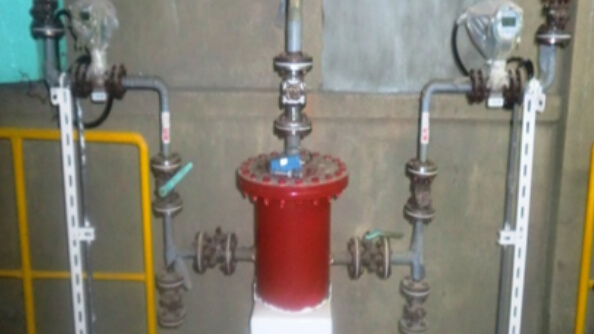
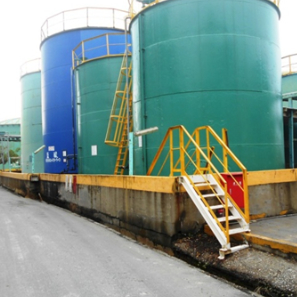
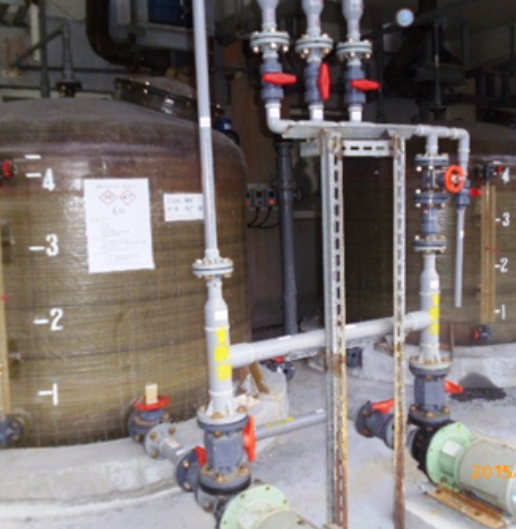
Employee safety
Management of hazardous materials
In accordance with Article 10 of the Occupational Safety and Health Law, with reference to hazardous chemical labeling and general knowledge rules and specific chemical substance hazard prevention standards, a "hazard general knowledge plan" has been formulated to manage and control various dangerous and hazardous substances. For hazardous chemicals (sulfuric acid, hydrochloric acid), storage tanks, pipelines and pipe valves are marked, and a list is prepared and safety data sheets are disclosed. There are overflow dikes and emergency leak alarms around the storage tank area to ensure Manage hazardous chemicals. And in accordance with the "Priority Management Chemical Designation and Operation Management Measures", complete the report for reference.
The transportation and loading and unloading of hazardous substances (sulfuric acid, hydrochloric acid) are stipulated in the seventh section of the “Safety and Hygiene Code of Practice” and the eighth section of the Code of Practice for Specific Chemical Substances of the Suao Plant. Carrying tank trucks need to be inspected and qualified by the traffic supervision unit. Drivers can only engage in transportation operations if they have obtained a qualification certificate in accordance with Article 3 of the "Administrative Measures for Professional Training of Road Transporters of Dangerous Goods. In addition, in accordance with Article 16 of the "Hazardous Chemical Labeling and General Information Rules", after vehicles carrying hazardous chemicals enter the workplace, relevant trained personnel should be designated to confirm that they have the labeling and The safety data sheet must be unloaded, transported, handled or used. In addition, in accordance with Article 84 of the Road Traffic Safety Regulations, vehicles carrying dangerous goods shall comply with the second clause: It is stipulated that dangerous goods signs and nameplates should be hung or pasted on the left, right and rear of vehicles carrying dangerous goods, and their contents And should list important items such as dangerous and hazardous materials labeling. To ensure that the transportation of hazardous materials (sulfuric acid, hydrochloric acid) is safe and smoothly completed.
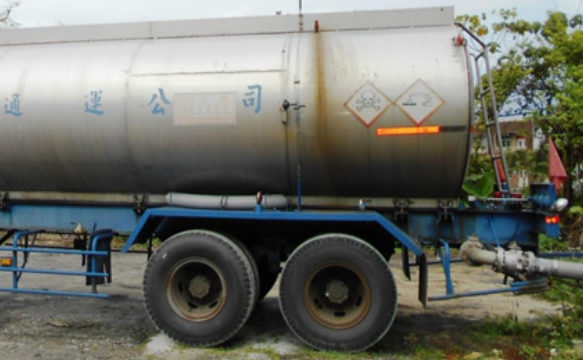
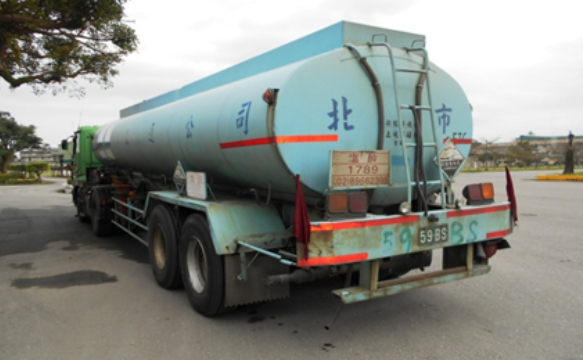
Emergency response mechanism
When natural disasters, fires and explosions, chemical or tank truck leaks occur inside and outside the factory, use various disaster relief resources, manpower and equipment to quickly deal with them to prevent the expansion of the disaster and reduce the loss of the accident to the factory, personnel and the natural environment , For the purpose of implementing the emergency response mechanism.
The company implements disaster prevention and rescue drills in accordance with laws and regulations, simulates emergency response measures when leakage occurs inside and outside the factory, and does various disaster prevention and rescue actions; establishes a mutual assistance and cooperation system to facilitate contact and mutual support channels for accidents. In addition, through education, training and drills, the applicability and feasibility of the effectiveness of accident notification and response measures are evaluated, so that emergency response units and support units are familiar with the roles and functions of the rescue process.
The Suao Plant of the company is a member of the Yilan Team of the National Drug Disaster Joint Prevention Organization of the Environmental Protection Agency of the Executive Yuan. It cooperates with the Environmental Protection Agency, the Drug Disaster Consultation Center and other units to support and coordinate the emergency response and rescue operations of chemical disasters in Yilan. It also provided existing venues for regional fire brigades for disaster relief and fire fighting education and training. Using the usual participation in joint defense drills and education training observations helped the company's members to improve their emergency response capabilities.
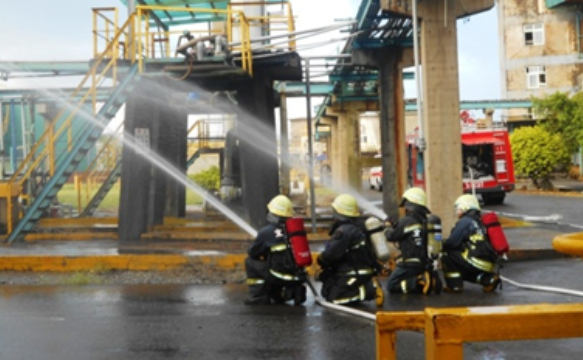

The Implementation of Emergency Drill and Education Training Record Form in 2019
Implementation date | Exercise project | Content description |
---|---|---|
2020.06.16 | Emergency response and process drill | Education and training content: 1. Type of disaster. 2. The focus of emergency response. 3. Emergency preparation and response management operating procedures. 4. Emergency missions are organized and managed. |
2020.06.11 | Chemical spill drill | Highlights of the exercise include: 1. The notification process after a leak occurs. 2. Disaster rescue for phased response. 3. Essentials for wearing protective gear. |
2020.09.15 | Overall rehearsal of poison leakage | Leakage status of toxic chemical material storage area: After the leakage of poisonous materials, the on-site personnel should immediately notify the unit supervisor and the on-site unit supervisor to understand, and then the unit supervisor announces the establishment of an emergency response team. |
2020.10.12(liquid caustic soda) 2020.11.25(hydrochloric acid) 2020.10.12 (Sulfuric acid) |
Transport of dangerous goods | Education and training content: 1. Safety standards for storage and transportation of dangerous goods. 2. Safety rules for loading and unloading hazardous materials. 3. Safety design of tank truck. 4. Crisis handling of dangerous goods. |
2020.06.11 2020.12.17 |
Fire education training and emergency drills | Highlights of the exercise include: 1. Description of fire case. 2. Exercising the use of fire extinguishers and hydrants. 3. Personnel evacuation drill. |
Social participation
Paying attention to the community and becoming a partner who grows with the community can create a win-win situation, and can be connected with the company's sustainable growth. At the beginning of the establishment of the factory, each operation site is evaluated for community impact and continues to negotiate with the community, and Long-term investment in community development plans and other activities to achieve our mission of social care.
We firmly believe that environmental protection and industrial development can coexist. Employees, quality, suppliers, plant safety, or community development are closely related. They are all part of corporate social responsibility and part of the company's competitiveness. The company is a traditional chemical manufacturing industry. With the concept of "take from the earth and use it for the land", we have always managed and practiced environmental protection, safety and health, and strived to win the recognition of the community and give back to the society.
Labour Relations
Staff structure
The company provides fair employment opportunities, and is committed to promoting a compatible and diverse environment. It also actively takes affirmative actions to provide equal employment and promotion opportunities for all job seekers. We categorize employees according to their employment types, employment contracts and operating locations, and clearly disclose the company's human resources information for 2020 as follows:
Job Title | Nationality | Name | Holding concurrent positions in other companie |
---|---|---|---|
CEO | Republic of China | Gordon Hwang | Director, Zai Fong Auto Transportation Co. Ltd. Director, East Tender Optoelectronics Co. Hsin Tender Co. Ltd. |
VP of Admin. | Republic of China | George Liu | Director, Zai Fong Auto Transportation Co. Ltd. Director, East Tender Optoelectronics Co. Supervisor, E-TTEQ Co. |
VP, Suao Plant | Republic of China | Leo Lin | N/A |
G.M Suao Plant | Republic of China | Stone Shih | N/A |
VP of Foreign Department | Republic of China | Chen Yi-Te | Chairman of Yukari Group Co., Ltd. Chairman of Sincere Industrial Corp. President of Zheng Bang Investment Co., Ltd |
AVP, Sales | Republic of China | Shuyuan Lin | N/A |
Manager, Finance Departmen | Republic of China | Jessica Chen | Director, Yukari Group Co. Ltd. |
Manager, Accounting Department | Republic of China | Ella Chu | Director, Yukari Group Co. Ltd. |
Audit Manage | Republic of China | Yen Lee | N/A |
Project | Male | Female | Total | |||
---|---|---|---|---|---|---|
Number of people | Percent% | Number of people | Percent% | Number of people | Percent% | |
Employee from Taiwa | 125 | 78.62% | 28 | 17.61% | 153 | 96.23% |
Foreign Employee | 6 | 3.77% | 0 | 0.00% | 6 | 3.77% |
Total | 131 | 82.39% | 28 | 17.61% | 159 | 100.00% |
Location | Male | Female | Total | |||
---|---|---|---|---|---|---|
Number of people | Percent% | Number of people | Percent% | Number of people | Percent% | |
Headquarter | 15 | 9.43% | 23 | 14.46% | 38 | 23.90% |
Suao Main Factory | 109 | 68.55% | 3 | 1.89% | 112 | 70.44% |
Changhua Factory | 4 | 2.52% | 1 | 0.63% | 5 | 3.14% |
Taichung Factory | 3 | 1.89% | 1 | 0.63% | 4 | 2.52% |
Total | 131 | 82.39% | 28 | 17.61% | 159 | 100.00% |
Employee salary
The company has equal pay for men and women for equal work. According to the Labor Standards Law, the salary level is above the basic salary. It does not discriminate against gender and does not have to work overtime. The benefits, working system, and working environment are all above the industry average. Labor and management coexist and prosper. Willing to serve the company.
Staff salary related expenses in the past three years
Unit: Thousands of New Taiwan Dollars
Project | 2018 | 2019 | 2020 |
---|---|---|---|
Salary expenses | 128,314 | 125,996 | 123,988 |
Labor health insurance expenses | 10,861 | 11,203 | 11,090 |
Pension expenses | 6,164 | 4,830 | 6,417 |
Other employee benefits | 7,052 | 7,128 | 6,900 |
Total | 172,299 | 149,157 | 148,395 |
Non-executive Number of full-time employees (unit: person) |
---|
137 |
Non-executive Average salary of full-time employees (Annual salary, unit: New Taiwan dollar) |
---|
758,342 |
Non-executive Median full-time employee salary (Annual salary, unit: New Taiwan dollar)) |
---|
512,384 |
Employee Benefits
The company has always regarded its employees as its greatest asset, and hopes to attract outstanding talents to join the Sesoda Co., Ltd. team through a market-competitive salary system, and promises to provide a high-quality work stage and challenging tasks to cultivate and lead a group Excellent talents who agree with the company's mission, vision and core values will move towards the goal of success together.
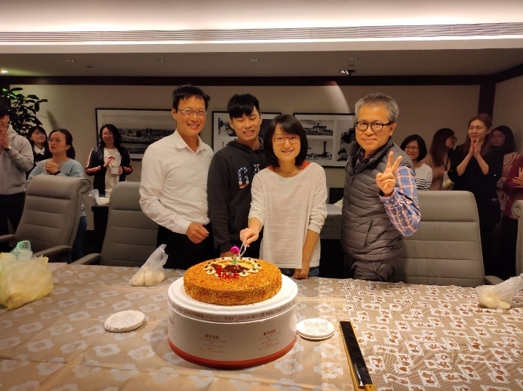
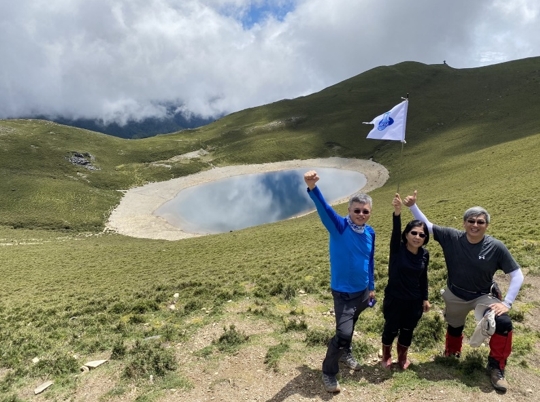
- The company has a professional labor union, which holds labor-management meetings every three months to establish a bridge for labor-employment response, communication, coordination and resolution, and announces relevant information through the internal network.
- In addition to the company's full compliance with the provisions of the Labor Standards Law, the company's articles of association specify that employees' remuneration is 4.5% of the year's profit, which is significantly better than the general level of traditional industries. Celebration, comfort, etc.
- In order to assist employees in taking care of their careers and families, the system has been implemented since 2006. Employees can receive a leave-of-work allowance of 60% of the labor insurance insured salary during their stay in employment in accordance with the Employment Insurance Law. It also provides family care leave, paternity leave for men, and physiological leave for women. The principle of choosing the right talent for the selection of education and retention is the principle, and there is no discrimination due to factors such as race, gender, marital status, age, political position or religious belief.
- The company has established employee retirement measures in accordance with the Labor Standards Law, and in conjunction with the implementation of the amendments to the Labor Retirement Regulations, revised the employee retirement measures on August 23, 2005. From July 1, 2005, employees who originally applied the old system can choose according to their personal wishes The old system or the new system, if the service years of the new system are selected or the employees who take up the job after the implementation of the new system, their service years are changed to a definite allocation system, and the pension payment is paid by the company on a monthly basis with a monthly salary of not less than 6% Funds are stored in the individual labor pension accounts. For the employees who choose the old system, the company according to the employee retirement method, according to the law, allocates employee pensions on a monthly basis and deposits them in the special pension account of Bank of Taiwan.
Staff education and training
To meet the needs of company development and manpower planning, enhance employees' knowledge, attitudes and skills required for team and individual work goals, promote employee productivity and work quality, enhance corporate profitability and brand image, and assist employees to strengthen their employ ability, The company provides complete staff training to achieve the above goals.
Training items | Training item description |
---|---|
Professional training | Refers to the professional education and training provided by various units to in-service employees, which focus on the improvement of professional work knowledge and technical level |
Generic training | In order to train and improve the knowledge, attitudes and skills common to the company's core values, culture, and goals, it also includes courses on language, computers, new knowledge lectures, mental health, laws and occupational safety. |
Self-inspired training | Provide books, training materials, professional journals, magazines, audio (video) files, teaching CDs, etc. for employees to self-study and further study after get off work or leisure. |
Class training | In order to cultivate and enhance the functions required by employees at all levels, the main purpose is to enhance the management capabilities, knowledge, and skills of employees at all levels, and to open up future career horizons. |
Pre-employment training for new recruits | Common pre-employment education and training provide new employees with introduction to the company's organization, history, business philosophy, corporate culture, personnel and welfare systems, management regulations, environment and products. |
Other training | The training courses needed for the operation and development of the company. |
2020 Statistics on the average training hours of each employee of the company
Category | Average traning hours(hr/year) | ||
---|---|---|---|
General Staff | M | 1 | Total: 75HR |
F | 2 | ||
Management class | M | 6 | Total: 68HR |
F | 4 |
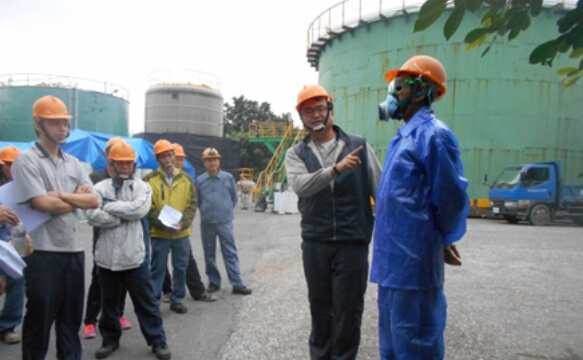
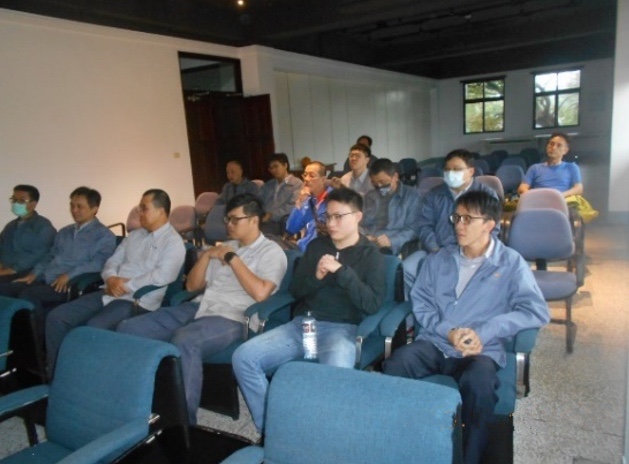
Employee health promotion and management
- Labor Health Service Plan: In accordance with the provisions of the Occupational Safety and Health Law and the Labor Health Protection Regulations, new laborers submit physical examination forms and perform job selection; in-service laborers perform general periodic health checks and labor health checks for work that particularly endangers health. Implement hierarchical management based on the inspection report, adjust the nature of the work appropriately according to the health situation, and hire a special doctor on-site service mechanism.
- Protections against abnormal working hours, human factors engineering, workplace violence, etc.: According to the Occupational Safety and Health Law, there is an "abnormal workload-induced disease prevention plan". Risk assessment and demand surveys are implemented through scales, and relevant databases are built for implementation. By comparison, appropriate treatment of at-risk laborers will be provided, and seminars on workplace violence prevention will be arranged to help prevent illegal violations in the workplace.
- Employee health promotion activities: The company plans health promotion activities such as health lectures, sports club activities, mental health lectures, and psychological counseling on employee care programs, so that workers can work in a safe environment and gain physical and mental health.
- Maternal Health Protection Plan for Female Workers: According to the Occupational Safety and Health Law, there are "Working Procedures for Female Workers' Maternal Health Protection". Appropriate arrangements for work after the assessment to protect women and maternal labor.